Polylactic acid (PLA) is a biodegradable plastic material used in many products spanning from 3D printing filament to food packaging. Customers have found that PLA is brittle and easily snaps while in use. PLA readily absorbs moisture from the air which leads to its structure breaking down, easily cracking especially in humid environments. Loop Co2’s technology has an advanced model designed to address these issues.
PLA is derived from annually renewable resources such as corn starch or sugarcane, making it a sustainable alternative to traditional petroleum-based plastics. Its biodegradable nature allows it to decompose into carbon dioxide and water under controlled composting conditions, typically within a few months. This characteristic aligns well with the principles of a circular economy, where materials are designed to be reused and recycled as much as possible, reducing waste and the environmental impact associated with traditional plastics. In the context of a circular economy, Loop CO2’s PLA product offers several end-of-life options that contribute to sustainability. For instance, PLA products can be composted, allowing the carbon sequestered during the growth of the plant feedstocks to be returned to the soil. This approach not only reduces plastic waste but also supports the diversion of biowaste from landfills and incineration, enhancing the efficiency of biowaste collection and reducing contamination in the waste stream.

Challenges
PLA exhibits a duality in its thermal properties. Its relatively low melting point is a boon for 3D printing enthusiasts, allowing for easier extrusion and manipulation during the printing process. However, this same characteristic renders PLA vulnerable to thermal degradation when exposed to elevated temperatures for extended periods. When subjected to high temperatures, PLA undergoes a softening phase, followed by re-hardening. This thermal cycling can induce changes in the polymer’s molecular structure, resulting in increased brittleness and diminished mechanical properties. Compounding this thermal sensitivity is PLA’s susceptibility to hydrolysis. Water molecules act as catalysts in breaking down the polymer chains that constitute PLA’s structure. This process, known as hydrolytic degradation, leads to a progressive weakening of the material. In environments with high humidity or when storage conditions are suboptimal, this degradation can accelerate, potentially rendering the filament unsuitable for high-quality prints.
As PLA naturally ages, degradation can be accelerated by exposure to UV light and lead to the breakdown of its molecular bonds. UV high-energy photons has the capacity to induce photochemical reactions within the polymer matrix of PLA. These reactions typically manifest as scission of the molecular bonds that form the backbone of the polymer chains. This stunts elasticity and increases its brittleness.
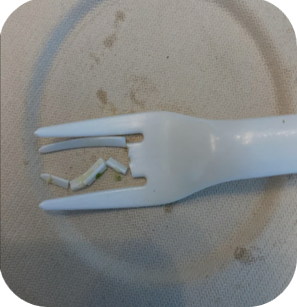
Loop CO2’s Solution
This is where Loop CO2’s innovation comes in; polyDEtP is an engineered material created from a new type of CO2 biobutadine monomer. Around 29% is composed of CO2 and 71% is butadiene. PolyDEtp enhances PLA’s properties due to the new chemical makeup, upgrading PLAs points of fracture and melting. PolyDEtP bonds to PLA to make it a stronger, more durable material that will not break or fragment when being used for the products it was created for. This evolved product not only guarantees long service life but does the favor of recycling carbon dioxide from the atmosphere into modern day use in a product- reaching a carbon neutrality all the while.
The market volume for PLA has been limited by one key material weakness: brittleness. While PLA is a promising bioplastic, its lack of flexibility and impact resistance has restricted its use to a narrow range of applications, preventing it from replacing many fossil-based plastics in broader industries. Loop CO2 addresses this challenge with breakthrough chemistry that introduces a soft, amorphous polyester into the PLA matrix. This innovation dramatically improves the toughness and flexibility of PLA, making it suitable for applications that demand higher performance—such as those currently served by expanded polystyrene and PVC. By removing a major barrier to PLA adoption, Loop CO2 places PLA in a far stronger position to replace conventional plastics, expanding its market potential. At the same time, the materials remain aligned with global sustainability goals by supporting recyclability and compostability, helping to drive the transition toward a circular economy.